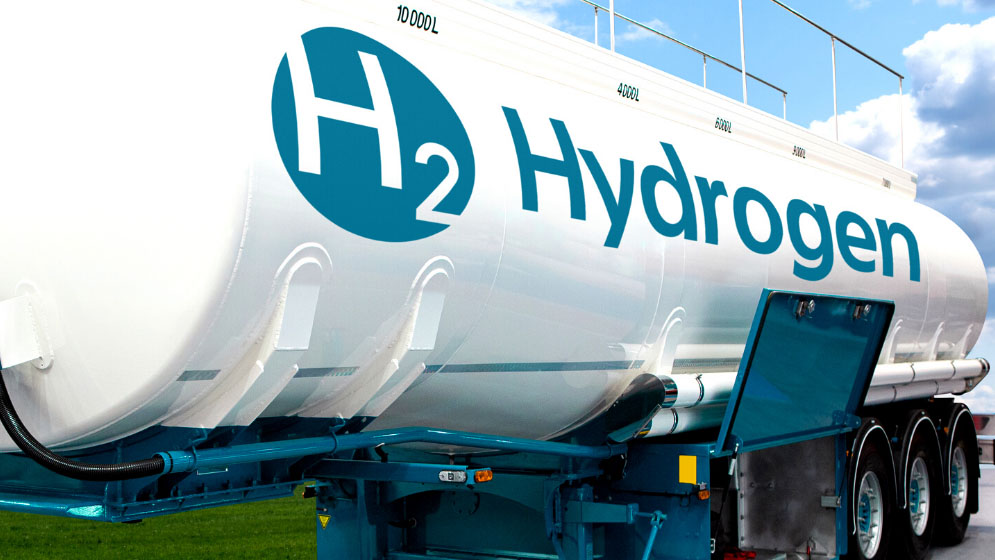
Kathairos has emerged as the leading North American solution for methane elimination from pneumatics, with more than 1,000 systems in operation across North America and over 40 major oil and gas producer partners.
In this post
More and more, hydrogen is being heralded as the new super fuel to combat climate change.
It is a sustainable energy source that does not produce CO2 emissions, and existing gas stations can be retrofitted into hydrogen refuelling stations to take advantage of existing infrastructure.
So why aren’t we all speeding full steam ahead on the hydrogen train?
Well, there are technical obstacles to overcome before hydrogen becomes a practical alternative to existing technologies. Chief among the barriers to widespread adoption of a hydrogen economy? The cost of hydrogen storage and transportation.
A new technique coming out of North Carolina may just be the solution we’ve been missing.
THE TRANSPORT PROBLEM
Despite its benefits, hydrogen gas is extremely reactive and needs to be transported with great care via a liquid carrier.
The main problem with this? Extracting hydrogen from the liquid carrier at destination sites, including fueling stations, is energy-intensive and expensive.
This process involves using something known as a photocatalyst to release hydrogen gas using sunlight. However, existing techniques are laborious, time-intensive and require significant amounts of rhodium, which is a very costly metal.
But is there a solution in sight?
Researchers from North Carolina State University have developed a novel technique for extracting hydrogen gas which is faster, less expensive and more energy efficient than previous approaches.
"We've developed a technique that applies a reusable photocatalyst and sunlight to extract hydrogen gas from its liquid carrier more quickly and using less rhodium, making the entire process significantly less expensive," remarks Malek Ibrahim, one of the authors of the paper and a former postdoctoral researcher at North Carolina State University. "What's more, the only by-products are hydrogen gas and the liquid carrier itself, which can be reused repeatedly. It's very sustainable."
OLD DOG, NEW TRICKS
The researchers attribute a key success of the new technique to the fact that the system is a continuous-flow reactor.
This reactor resembles a thin, clear tube packed with “sand, consisting of very small grains of titanium oxide. Hydrogen-carrying liquid is pumped into one end of the tube, and rhodium-coated particles line the outside of the tube where they are exposed to sunlight.
Because the rhodium-coated exterior is extremely photosensitive, it reacts with the liquid carrier in the presence of sunlight to release hydrogen molecules as a gas.
The new technique ensures that rhodium only coats the outer particles, drastically reducing the need for rhodium particles: while conventional reactors typically contain 1% rhodium, the continuous flow reactor only needs 0.025% rhodium in order to function effectively.
Given that a single gram of rhodium costs over $500, this reduction represents a significant cut to total costs associated with the system.
The prototype reactor achieved a remarkable 99% yield, meaning that all but 1% of the hydrogen molecules within the liquid carrier were released. Even more impressive? This was done in three hours, which is 8x faster than conventional batch reactors, which can take up to 24 hours to reach the same yield.
The system should also be fairly easy to scale up or scale out for commercial reuse by making the tube longer or merging multiple tubs in parallel fashion. A simple six-hour cleaning process can “regenerate” the catalyst after 72 hours of continuous use, when it starts to decrease in efficacy. Following this, the system can be restarted and run at full efficiency for another 72 hours.
The road to a hydrogen economy may be long, but who knows- maybe we finally have the roadmap to get there.
Explore more posts from Kathairos
.jpg)
Decarb Digest, Issue 01: Discover Why Energy Leaders Aren’t Waiting on Washington
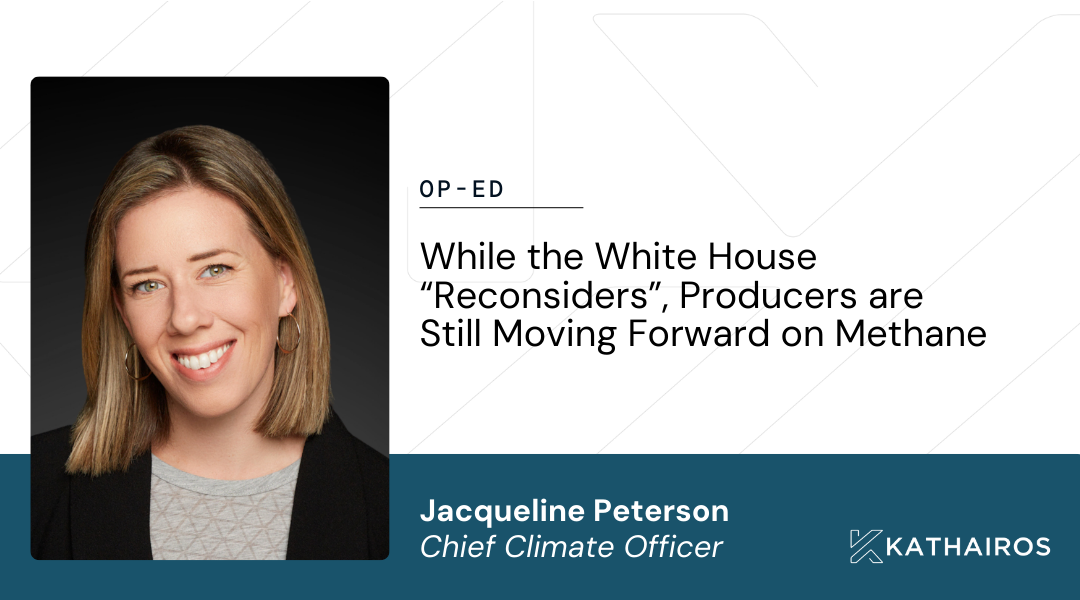
Op-Ed: While the White House “reconsiders”, producers are still moving forward on methane
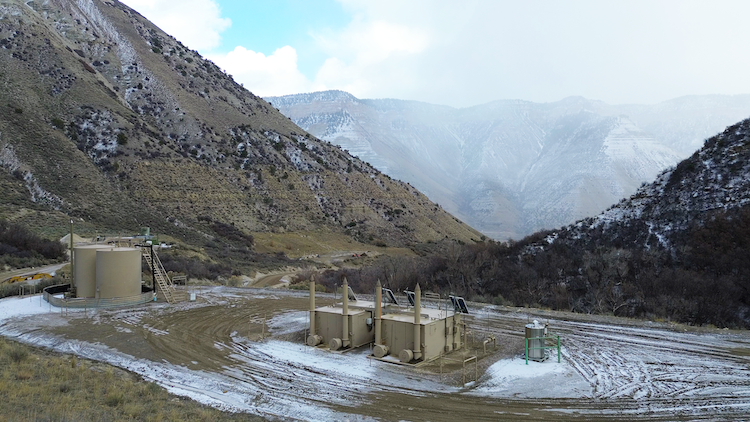